CARBON BLACK
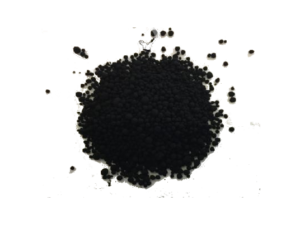
Carbon black, obtained by various methods (furnace, thermal, acetylene, channel etc.), is consitituted by carbon being a product of partial thermal decomposition of hydrocarbons.
Since decades carbon black paid attention of scientists and maufacturing companies because of its favourable properties as a rubber goods filler (so-called reinforcing filler). Incorporating of CB entails obtaining of homogenous, black coloured rubber compounds with parallel enhancement of rigidity and fracture resistance of the vulcanizates. Tremendous impact of the blacks has been reflected in the classification of the grades on the basis of intrinsic parameters (manufacturing method, average particles size, specific surface area, pH and so forth). In example, particle diameters may vary from 20 nm in case of some furnace blacks up to several hundreds nm for thermal ones. These particles inherently arrange into aggregates, viz. the smallest individuals dispersible in polymer matrix (having sizes up to microns) and bigger agglomerates (e.g pellets of magnitude of few milimeters).
Appropriate legislative actions had to be taken due to the presence of organic impurities (mainly PAH), absorbed on the CB surface. These naturally occur as a by-product of partial combustion. As a result, carbon black producers began to to implement alternative routes of syntheses, along with more strict control over processes being carried out. In spite of organic residues do not significantly influence on reinforcing characteristics of black, environmental issues and health hazards play the crucial roles. As of inorganic impurities, which are resultant of final manufacturing stages, they are often find to favour rate of curing, being higher for high pH of carbon black. Besides that, concentration of oxygen-containing moieties on the surface and unsaturated bonds corresponds to the way how rubber curing proceeds.
Wide assortment of carbon blacks offered by Polsaros Sp. z o.o. (conventional, specialty, odourless, pyrolytic), guarantees effective choice accoriding to Customers needs. Each grade fulfills the highest standards, as advocated in international and technical norms, as well as in law regulations and legislation.
Conventional carbon black acc. to ASTM D 1765
N115 | N134 | N220 | N234 | N326 | N330 | N339 | N375 | N550 | N660 | N772 | N774 | |||
Parameter | Unit | Test method | ||||||||||||
STSA | 103 m2/kg | ASTM D-6556 | 124±5 | 137±5 | 106±5 | 112±5 | 76±5 | 75±5 | 88±5 | 91±5 | 39±5 | 34±5 | 30±5 | 29±5 |
NSA | 103 m2/kg | ASTM D-6556 | 137±5 | 143±5 | 114±5 | 119±5 | 78±5 | 78±5 | 91±5 | 93±5 | 40±5 | 35±5 | 32±5 | 30±5 |
Iodine Adsorption No. | g/kg | ASTM D-1510 | 160±5 | 142±5 | 121±5 | 120±5 | 82±5 | 82±5 | 90±5 | 90±5 | 43±5 | 36±5 | 30±5 | 29±5 |
Oil Adsorption No. | 10-5 m3/kg | ASTM D-2414 | 113±5 | 127±5 | 114±5 | 125±5 | 72±5 | 102±5 | 120±5 | 114±5 | 121±5 | 90±5 | 65±5 | 72±5 |
COAN | 10-5 m3/kg | ASTM D-3493 | 97±5 | 103±5 | 98±5 | 102±5 | 68±5 | 88±5 | 99±5 | 96±5 | 85±5 | 74±5 | 59±5 | 63±5 |
Ash content | %, max. | ASTM D-1506 | 1,0 | 1,0 | 1,0 | 1,0 | 1,0 | 1,0 | 1,0 | 1,0 | 1,0 | 1,0 | 1,0 | 1,0 |
Tint strength | – | ASTM D-3265 | 123±5 | 131±5 | 116±5 | 123±5 | 111±5 | 104±5 | 111±5 | 114±5 | – | – | – | – |
Residue on sieve, #325 | %, max. | ASTM D-1514 | 0,05 | 0,05 | 0,05 | 0,05 | 0,05 | 0,05 | 0,05 | 0,05 | 0,05 | 0,05 | 0,05 | 0,05 |
Residue on sieve, #35 | %, max. | ASTM D-1514 | 0,001 | 0,001 | 0,001 | 0,001 | 0,001 | 0,001 | 0,001 | 0,001 | 0,001 | 0,001 | 0,001 | 0,001 |
Heating loss big bag paper bag | %, max. | ASTM D-1509 | 1,5 2,5 | 1,5 2,5 | 1,5 2,5 | 1,5 2,5 | 1,5 2,5 | 1,5 2,5 | 1,5 2,5 | 1,5 2,5 | 1,5 2,5 | 1,5 2,5 | 1,5 2,5 | 1,5 2,5 |
pH | – | ASTM D-1512 | 6 – 9 | 6 – 9 | 6 – 9 | 6 – 9 | 6 – 9 | 6 – 9 | 6 – 9 | 6 – 9 | 6 – 9 | 6 – 9 | 6 – 9 | 6 – 9 |
Fines content big bag paper bag | %, max. | ASTM D-1508 | 8,0 12,0 | 8,0 12,0 | 8,0 12,0 | 8,0 12,0 | 8,0 12,0 | 8,0 12,0 | 8,0 12,0 | 8,0 12,0 | 8,0 12,0 | 8,0 12,0 | 8,0 12,0 | 8,0 12,0 |
Average pellet hardness (of 20) | gf max. | ASTM D-5230 | 50,0 | 50,0 | 50,0 | 50,0 | 50,0 | 50,0 | 50,0 | 50,0 | 50,0 | 50,0 | 50,0 | 50,0 |
Indiv. max. pellet hardness | gf max. | ASTM D-5230 | 90,0 | 90,0 | 90,0 | 90,0 | 90,0 | 90,0 | 90,0 | 90,0 | 90,0 | 90,0 | 90,0 | 90,0 |
Bulk density | kg/m3 | ASTM D-1513 | 345±25 | 320±25 | 355±25 | 320±25 | 455±25 | 380±25 | 345±25 | 345±25 | 360±25 | 440±25 | 520±25 | 490±25 |
Toluene discoloration | %, min. | ASTM D-1618 | 80,0 | 80,0 | 80,0 | 80,0 | 80,0 | 80,0 | 80,0 | 80,0 | 80,0 | 80,0 | 60,0 | 60,0 |
Pyrolytic carbon black
One of the many possibilities how to utilize pyrolytic carbon black is manufacturing of activated charcoal. It is also applied as an igredient of pigments used in textiles, production of leather, fur, paper, small-scale chemicals, plastics, other non-metal mineral goods such as plasters, cements. As an important raw material in large-scale chemical industry including petroleum based substances, non-noble metals, end use metal commodities, excluding devices and machines. Pyrolytic grades play essential role in fire resistant products, as a reinforcing filler in low quality rubber goods, part of road surface formulations and as potential solid fuel with high calorie content.
Total dioxines, PCB, PCP and furanes content acc. to MAS_PA002 is below detection level.
T30 | T30S | T35 | TR30 | TR30S | TR35 | |||
Parameter | Unit | Test method | ||||||
BET surface area | m2/g | ASTM D-6556 | 86 | 77 | 93 | 86 | 77 | 93 |
STSA | m2/g | ASTM D-6556 | 69 | 62 | 77 | 69 | 62 | 77 |
Oil Adsorption No. | cc/100g | ASTM D-2414 | 96 | 88 | 83 | 96 | 88 | 83 |
Aver. primary particle size | nm | TEM | 30-35 | 30-35 | 30-35 | 30-35 | 30-35 | 30-35 |
Specific gravity | g/cm3 | – | 1,86 | 1,86 | 1,86 | 1,86 | 1,86 | 1,86 |
Residual hydrocarbon volatile content | % | TGA | – | – | 1,0 | – | – | 1,0 |
Moisture content | %, max. | ASTM D-1509 | 1 | 1 | 1 | 1 | 1 | 1 |
Residue on sieve, 0,045 mm | %, max. | ASTM D-1514 | 0,1 | 0,1 | – | 0,1 | 0,1 | – |
Fines content, 0,125 mm | %, max. | ASTM D-1508 | 7 | 7 | – | 7 | 7 | – |
SiO2 content | % | ASTM D-1506 | 5-7 | 24-26 | 17 | 5-7 | 35 | 17 |
Bulk density | kg/m3 | ASTM D-1513 | 390 | 390 | 390 | 390 | 390 | 390 |
PAH content | ppm, max. | FDA met. 63 | 20 | 20 | 20 | 20 | 20 | 20 |
pH | – | ASTM D-1512 | 7,5-8,5 | 7,5-8,5 | 8,0 | 7,5-8,5 | 7,5-8,5 | 8,0 |
Average pellet hardness | g, max. | ASTM D-5230 | 55 | 55 | – | 55 | 55 | – |
Individual pellet hardness | g, max. | ASTM D-5230 | 85 | 85 | – | 85 | 85 | – |
MRG blacks of low grit – high purity (KLAREX RG)
RG 113 | RG 223 | RG 225 | RG 227 | RG 522 | |||
Parameter | Unit | Test method | |||||
Iodine Adsorption No. | g/kg | ASTM D-1510 | 43±5 | 43±5 | 44±5 | 28±5 | 32±5 |
STSA | m2/g | ASTM D-6556 | 38±5 | 40±5 | 40±5 | 27±5 | 31±5 |
Oil Adsorption No. | cc/100g | ASTM D-2414 | 111±5 | 123±5 | 123±5 | 120±5 | 52±5 |
COAN | cc/100g | ASTM D-3493 | 81±5 | 86±5 | 86±5 | 78±5 | 52±5 |
Heating loss (mat. packed) big bag paper bag | %, max. | D-1509 | 1,5 2,5 | 1,5 2,5 | 1,5 2,5 | 1,5 2,5 | 1,5 2,5 |
Residue on sieve, #325 | ppm | ASTM D-1514 | 15,0 max. | 15,0 max. | 8,0 max. | 15 max. | 25 max. |
Residue on sieve, #100 | ppm | ASTM D-1514 | 5,0 max. | 5,0 max. | 2,0 max. | 5,0 max. | 2 max. |
Residue on sieve, #35 | ppm | ASTM D-1514 | 0 | 0 | 0 | 0 | 0 |
Ash content | %, max. | ASTM D-1506 | 0,3 | 0,3 | 0,3 | 0,2 | 0,2 |
Average pellet hardness (of 20) | gf max. | ASTM D-5230 | 25,0 max. | 25,0 max. | 25,0 max. | 20 max. | 25 max. |
Indiv. max. pellet hardness | gf max. | ASTM D-5230 | 60,0 max. | 60,0 max. | 60,0 max. | 60,0 max. | 60,0 max. |
Fines content big bag paper bag | %, max. | ASTM D-1508 | 8,0 12,0 | 8,0 12,0 | 8,0 12,0 | 8,0 12,0 | 8,0 12,0 |
Toluene discoloration | % | ASTM D-1618 | 80,0 min. | 80,0 min. | 80,0 min. | 80 min. | 80 min. |
Specialty CB (non-ASTM)
Thanks to selection of high quality raw materials of strictly controled supply base and exploitation of proper purification systems, specialty premium grades have been marketed beside carbon black designed for rubber goods (both technical and tire parts). They are sucessfully applied in inks, paints, polymer masterbatches (for fibres, non-wovens, coatings), wires and cables. Food contact approved grades are also available in our offer.
Electra 273 | Electra 274 | BARONX 12 | COLORX 22 | JETEX 115P | ONYX 636 | ONYX 640 | |||
Parameter | Unit | Test method | |||||||
Iodine Adsorption No. | mg/g | ASTM D-1510 | 41 | 70 | – | – | 80 | 125 | 130 |
STSA | m2/g | ASTM D-6556 | – | – | 30-40 | 112 | – | – | – |
Oil Adsorption No. | 10-5 m3/kg | ASTM D-2414 | 124 | 120 | 90 | 115 | 100 | 105 | 90 |
Tint strength (ITRB#3) | % | ASTM D-3265 | 55 | 65 | 65 | 116 | 100 | 103 | 108 |
Ash content | %, max. | ASTM D-1506 | 0,09 | 0,09 | – | – | 0,1 | – | – |
Residue on sieve, #325 | ppm, max. | ASTM D-1514 | 10 | 10 | 100 | 50 | 20 | 20 | 20 |
Moisture content | % max. | ASTM D-1509 | 0,60 | 0,60 | 5 | 3 | 1 | – | – |
Applications | – | – | wires & cables, conductive materials | wires & cables, conductive materials | coating materials | coating materials, flexo ink, masterbatches | pipes, articles intended for food contact, geomembranes | synthetic fibres | synthetic fibres |
If an appropriate grade fulfilling your requirements cannot be find, please kindly notice, that tables presented herein depicts the chosen ones only. We are able to meet any specific needs of the Customer.
COUNTRY OF ORIGIN:
India, Netherlands
Full technical documentation including technical specifications, safety data sheets, ISO certificates, REACH certificates and other regarding the product are available upon request. Please contact us.