PRECIPITATED SILICA
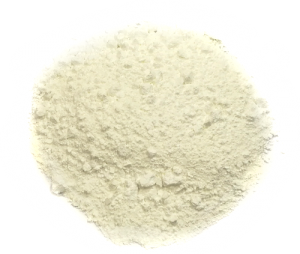
Precipitated silica is a form of synthetic amorphous silicon dioxide, being one of the purest forms of the mineral.
Its manufacturing process involves multistage neutralization of sodium silicate (water glass) solution with an acid (commercialy sulphuric). Silicic acid is generated at concentration greater than the solubility limit of silica, leading to its polymerization and precipitation out of solution. The physical properties of precipitated silica can be modified during the manufacturing process to provide products with a wide range of performance enhancing features designed for many different end uses. The most important factors affecting silica properties are the pH, the temperature, the residence time, the solid concentration, the rate of addition of raw materials, the stirring intensity and the feed position of the raw materials. Following precipitation, the silica is separated out of the suspension typically by filtration, washed to remove any impurities and dried. Finishing stage consists of milling, granulating, pelleting and, for example, switching to hydrophobicity.
As a raw material is widely used in many industries, including the rubber (in which everything has begun to develop since 1992, when Michelin patented very first silica filled tread rubber compound), electronics, pharmaceutical, manufacturing, cosmetics and agricultural.
Precipitated silica is used in the industry of:
• tire
• rubber
• footwear (CHECK NEW CATALOGUE – TYRE AND RUBBER)
• food & feed
• coatings, paints and inks
• adhesives and sealants
• agriculture (CHECK NEW CATALOGUE – FOOD FEED DETERGENTS).
Precipitated silica as a filler introduced into tread rubber compounds has been found to improve rolling resistance, wet grip and other dynamic properties, giving the tires reinforcing properties.
Polsaros offers the following grades of silica for tire and rubber applications.
Precipitated silica – granulated
Parameter | MFIL-60(G) | MFIL-80(G) | MFIL-90(G) | MFIL-100(G) | MFIL-125(G) | MFIL-150(G) | MFIL-175(G) | MFIL-200(G) |
Loss on drying (105°C, 2 hrs.), % | 4-7 | 4,5-7,5 | 4-8 | 3-7 | 4-7 | 4-7 | 4-7 | 3-7 |
Loss on ignition, anhydrous basis (1000°C), % | – | 7,0 maks. | 7,0 maks. | 3,0-6,0 | – | – | 6,0, maks. | 3,0-6,0 |
Bulk density (mat. tapped), g/L | 350 min. | 300-370 | 300-370 | 300-370 | – | 305-355 | 300-370 | 300-370 |
pH (5% aqueous slurry), – | 8,0-9,0 | 6,0-7,0 | 6,5-8,5 | 6,0-7,0 | 6,5-7,3 | 6,5-7,3 | 6,0-7,0 | 6,0-7,0 |
SiO2 content, anhydr. basis, %, min. | – | 98,5 | 98,5 | 98,5 | 98,0 | – | 98,5 | 98,5 |
BET surface area, m2/g | 40-70 | 70-90 | 75-110 | 100-130 | 115-135 | 115-135 | 160-190 | 170-190 |
CTAB surface area, m2/g | – | 65-85 | 65-95 | 90-120 | – | – | 157-177 | – |
Conductivity (4% water slurry), μS/cm, max. | 1300 | 1300 | 1300 | – | – | – | 1300 | – |
Impurities content, max. Fe, ppm Cu Mn soluble salts, % CaO Al2O3 | 500 10 10 | – | 200 1 | 200 1 | 6 35 2,0 0,5 | 2,0 0,5 0,75 | – | – |
Sieve analysis & fines content (int. method) retained on #50, % min. passed through #200, % max. passed through #325. % min. | – | – | – | – | 85,0 5,0 – | 85,0 5,0 99,5 | 85,0 5,0 – | – |
Precipitated silica – HDS, spray dried & milled
Parameter | MFIL-125(S) | MFIL-200(S) | MFIL-160(HDS)DF | MFIL-210(HDS)DF | MFIL-200(P) | MFIL-LV |
Appearance | Fine, white odorless powder free from signs of impurity | Fine, white odorless powder free from signs of impurity | Clean white micropearls | Clean white micropearls | Fine, white odorless powder free from signs of impurity | Fine, white odorless powder free from signs of impurity |
Loss on drying (105°C, 2 hrs.), % | <6,0 | <6,0 | 5-7 | 5-8 | <6,0 | <7,0 |
Loss on ignition, anhydrous basis (1000°C), % | <6,0 | <6,0 | – | – | <6,0 | <8,5 |
Bulk density (mat. packed), g/L | 230-270 | 230-270 | >230 | >230 | 80-130 | 130-160 |
pH (5% aqueous slurry), – | 6,0-7,0 | 6,0-7,0 | 6,0-7,0 | 6,0-7,0 | 6,0-7,0 | 6,5-7,5 |
SiO2 content, anhydr. basis, %, min. | 98,5 | 98,5 | 98,5 | 98,5 | 98,5 | 98,0 |
BET surface area, m2/g | 115-135 | 170-190 | 150-170 | 115-135 | 170-200 | 115-135 |
CTAB surface area, m2/g | – | – | 145-165 | 185-215 | – | – |
Water absorption, % min. DBP, cc/100g, min. | 230 220 | 240 240-260 | – | – | 240 250 | 160-180 – |
Impurities content, max. Fe, ppm soluble salts, % | 200 1,0 | 200 1,0 | 1,5 | 1,5 | 200 1,0 | 1,0 |
Sieve analysis & fines content (int. method) D50, μm retained on #325 (wet sieving), % max. | – | – | – | – | – 1,0 | 10-15 1,0 |
* HDS(DF) – highly dispersible silica dust free, S – spray dried, P & LV – milled
Considerable amounts of precipitated silica are being used in other branches of industry: food & feed – as a carrier for nutrients, anti-caking agent for free-flowing powders, defoamer; oral care, farmaceutics and cosmetics – ingredient in toothpastes, laundry detergents, as a carrier, absorbent of viscous liquids, thickener and abrasive agent; agricultural – pesticides; polymers, glues, paper, battery separators industries.
Precipitated silica for other applications
Parameter | MFIL-P | MFIL-P(U) | MFIL-P(U)DF | MFIL-TS117 (silane treated) |
Appearance | Fine, white odorless powder free from signs of impurity | Fine, white odorless powder free from signs of impurity | White odorless micro pearl silica free from signs of impurity. | Fine, white powder |
Loss on drying (105°C, 2 hrs.), % | <6,0 | <6,0 | <6,0 | <4,0 |
Loss on ignition, anhydrous basis (1000°C), % | <6,0 | <6,0 | <6,0 | <14,0 |
Bulk density (mat. packed), g/L | 80-130 | 230-270 | >240 | 120-180 |
pH (5% aqueous slurry), – | 6,0-7,0 | 6,0-7,0 | 6,0-7,0 | 7,0-9,0 |
SiO2 content, anhydr. basis, %, min. | 98,5 | 98,5 | 98,5 | 98,0 |
BET surface area, m2/g | >180 | 180-200 | 160-200 | – |
Water absorption, % min. DBP, cc/100g, min. | 260 220 | 240 250 | – 250 | – 220 |
Impurities content, max. Fe, ppm Pb, ppm As, ppm Hg, ppm soluble salts, % | 200 1,0 | 15,0 5,0 1,0 1,0 | 200 15,0 5,0 1,0 | 300 – – – 1,8 max. |
Sieve analysis & fines content (int. method) D50, μm retianed on #325 (wet sieving), % max. | – 1,0 | 110 – | 250-350 – | 12,0 max. 0,5 |
If an appropriate grade fulfilling your requirements cannot be find, please kindly notice, that tables presented herein depicts the chosen ones only. We are able to meet any specific needs of the Customer.
PACKAGING:
Silica is supplied in 25 kgs laminated HDPE bags with LDPE inserts or in 800 kg Big Bags. Depending on the needs, there is possibility to find other packaging solution upon Customer request. Shelf life of the products – one year from manufacturing date. Recommended storage of bags in sealed conditions only in a ventilated room at room temperature. No special storage conditions required (inert material).
COUNTRY OF ORIGIN:
Full technical documentation including technical specifications, safety data sheets, ISO certificates, REACH certificates and other regarding the product are available upon request. Please contact us.